Electroplating Surface Treatment Introduction

In an electroplating surface treatment, after the AC input voltage is filtered by a rectifier circuit, high-voltage DC power is obtained. The “variable frequency conversion” stage inverts this high-voltage direct current into approximately 30kHz high-frequency alternating current. This high-frequency AC is then transformed into secondary voltage via a high-frequency transformer and filtered through a high-frequency rectifier circuit to produce the required output voltage. The electroplating surface treatment employs a control circuit to sample output voltage and current. These sampled signals undergo closed-loop feedback to generate pulse width modulation (PWM) signals, which regulate the inverter circuit and maintain stable output voltage/current – a critical requirement for precision electroplating applications.
Types of Electroplating Surface Treatment
Surface treatment techniques play a vital role in improving material characteristics and prolonging operational lifespan, particularly for metals and polymers in industrial applications.These techniques rely on customized power conversion systems that adapt electrical energy to support various coating deposition technologies. Primary rectification systems fall into several key classifications:
These precision units deposit metallic coatings like copper, nickel, zinc, or gold onto target surfaces through controlled electrical processes. This technology simultaneously achieves three critical objectives: strengthening substrate durability against chemical corrosion and mechanical abrasion, while producing refined surface finishes. Equipment selection varies significantly – hard chrome rectifiers handle industrial-grade thickness requirements, polarity-reversing models optimize adhesion for complex geometries, and pulse rectifiers enable nanometer-level deposition control. Such capabilities make them indispensable across automotive component hardening, aerospace alloy treatments, and particularly in PCB manufacturing where micron-scale conductor patterning determines circuit reliability.
Designed to form protective oxide layers on materials such as aluminum. These rectifiers precisely regulate voltage and current during both anodizing and subsequent coloring stages to improve surface durability and appearance.
Employed in processes where particles are deposited onto substrates through an electric field, commonly used for coating plastics and metals with uniform layers.
Critical for plasma plating techniques involving high-temperature plasma jets. These rectifiers manage plasma parameters to ensure precise control over coating adhesion and quality, producing robust and long-lasting surface layers. By tailoring rectifier selection to specific needs, these systems optimize outcomes such as enhanced surface resistance, electrical conductivity, or decorative finishes while maintaining process efficiency.
Types of Electroplating:
Each electroplating technique serves a unique function, focusing on specific performance attributes. Here is an overview:
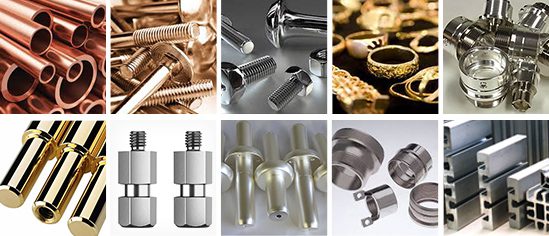
Chrome Plating and Hard Chrome Plating
Purpose: To provide exceptional hardness and corrosion resistance in electroplating surface treatment.
Tin Plating
Purpose: Utilized for its solderability and corrosion resistance in electroplating surface treatment.
Tin-Lead Plating
Purpose: Improves solderability. Trend: Phased out due to lead concerns; replaced by bright/matte tin alternatives.
Palladium-Nickel Plating
Purpose: Superior signal transmission and wear resistance vs. gold. Advantage: Combines palladium’s corrosion resistance with nickel’s hardness.
Copper Plating
Purpose: Enhances adhesion for subsequent layers and corrosion resistance. Note: Prone to oxidation (forms non-conductive copper oxide/green patina). Requires protective coatings.
Nickel Plating
Purpose: Used as a base layer or decorative finish; improves corrosion/wear resistance. Electroless nickel offers chrome-like durability. Note: Magnetic properties limit use in electronics (e.g., DIN/N connectors) to avoid signal interference.
Zinc Plating
Purpose: A cost-effective method for corrosion protection in electroplating surface treatment.
Gold Plating
Purpose: Optimizes conductive contact impedance and signal transmission. Key: High stability but costly.
Silver Plating
Purpose: Best conductivity and signal performance. Note: Conducts even when oxidized but tarnishes over time. Higher cost.
Selection Criteria
Match plating type to application needs: corrosion/wear resistance, conductivity, cost, and environmental regulations.
Role of Electroplating Surface Treatment

Protection Against Corrosion
– Shields metal surfaces from rust and chemical damage (e.g., zinc plating on steel).
Increased Wear Resistance
– Hard coatings (e.g., chromium plating) reduce friction and extend part life.
Improved Appearance
– Adds shiny, decorative finishes (e.g., gold plating on jewelry, chrome on car parts).
Better Electrical Conductivity
– Used in electronics (e.g., copper plating on circuit boards).
Enhanced Solderability
– Improves bonding in electronic components (e.g., tin plating).
Repair of Worn Parts
– Restores dimensions and functionality (e.g., rebuilding engine components).
Special Industrial Uses
– Provides heat resistance (e.g., nickel plating in aerospace).
– Used in medical devices (e.g., biocompatible coatings).
Electroplating Surface Treatment process

This multi-stage process ensures durable, high-performance metal coatings through precise control at each phase:
Pre-treatment
Workpieces undergo thorough cleaning (mechanical, chemical, or ultrasonic) to eliminate contaminants like oils and oxides. Subsequent grinding/etching creates uniform surfaces, while activation treatments (acid/alkaline solutions) optimize substrate receptivity.Plating Execution
A precisely formulated electrolyte solution containing metal salts and additives enables controlled deposition. Operators select appropriate metals (chromium, nickel, zinc, etc.) and adjust current density (0.5-15 A/dm² typical) based on desired coating characteristics. Critical parameters include solution temperature (20-60°C) and pH balance (1-13 range depending on process).Post-treatment
Coated components undergo deionized water rinsing to remove residual chemicals. Quality verification includes thickness measurement (XRF/eddy current), adhesion testing (tape/scratch methods), and corrosion resistance assessment (salt spray testing). Approved items receive protective packaging.
Troubleshooting Guide
Pinholes: Improve degassing/pretreatment cleanliness
Delamination: Optimize current density/surface activation
Blistering: Adjust agitation/voltage parameters
This systematic approach balances deposition efficiency with coating integrity, requiring vigilant parameter monitoring and contamination control throughout the cycle.
Advantages of Liyuan Haina Electroplating Rectifiers
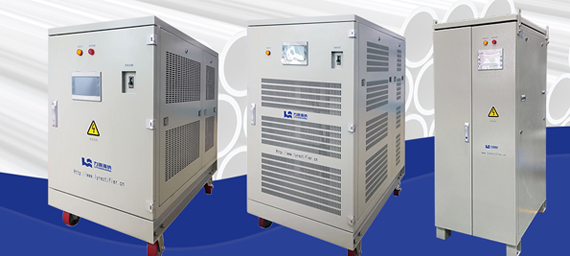
Flexible Output Waveform Modulation
From jewelry micro-gold plating to ship propeller nickel-cobalt alloys, operators dial in pulse settings like seasoned chefs seasoning a dish. Need to plate 0.3μm copper traces on circuit boards without dendrites? Crank the frequency to 2,500Hz with 10% duty cycle. Battling pitting on hydraulic valve stems? A 50ms reverse pulse every third cycle acts like a micro-scrub brush. This isn't just "adjustable" – it's handing a Swiss Army knife to electroplating engineers.
Excellent Energy-Saving Effect
The rectifier delivers high efficiency by converting AC to DC power with minimal energy loss during operation. This design significantly reduces electricity consumption, offering substantial cost benefits for large facilities requiring continuous electroplating processes.
High Output Stability
The rectifier actively compensates for load shifts or input voltage swings, holding DC output within ±1% tolerance. In high-volume nickel plating lines, this precision prevents edge buildup or thin spots, ensuring every batch meets automotive OEM specifications. Even during 24/7 operation, performance remains rock-solid.
Ease of Waveform Modulation
Operators achieve precise control via user-friendly controls or automated systems, enabling rapid and accurate waveform adjustments. This simplifies fine-tuning of plating parameters, streamlining workflow while maintaining precision.
These features collectively make Liyuan Haina rectifiers indispensable for energy-efficient, high-quality electroplating operations across industrial applications.
Electroplating Surface Treatment Application
The Plating Rectifier Equipment series of electroplating rectifiers is extensively utilized for a variety of surface treatments, including PCB electroplating, hard chrome coating, as well as plating with copper, nickel, zinc, gold, and silver, among other hardware surface treatment applications.
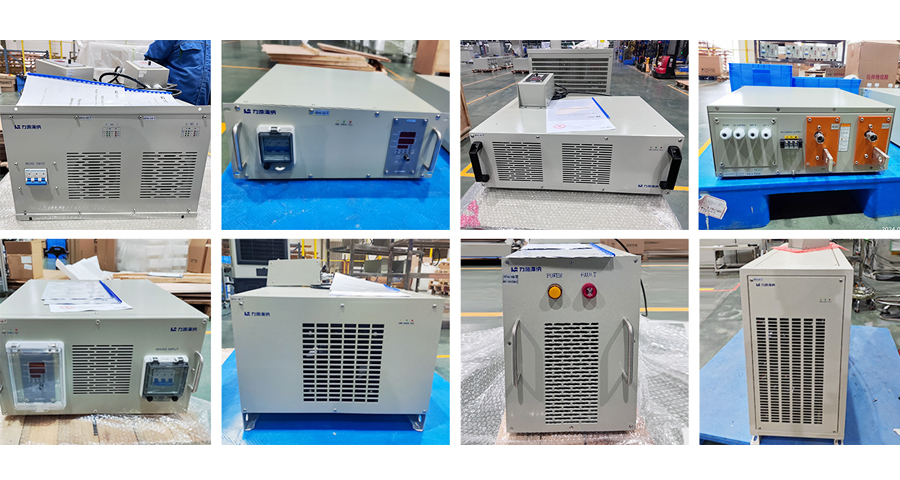
Field application diagram
Our products are also exported to the United States, Canada, Britain, Italy, England, Spain, South Africa, Russia, UAE, Japan, South Korea, Malaysia and other parts of the world.
Industry application examples
Automobile industry,ABS material surface treatment,Copper, nickel, chromium
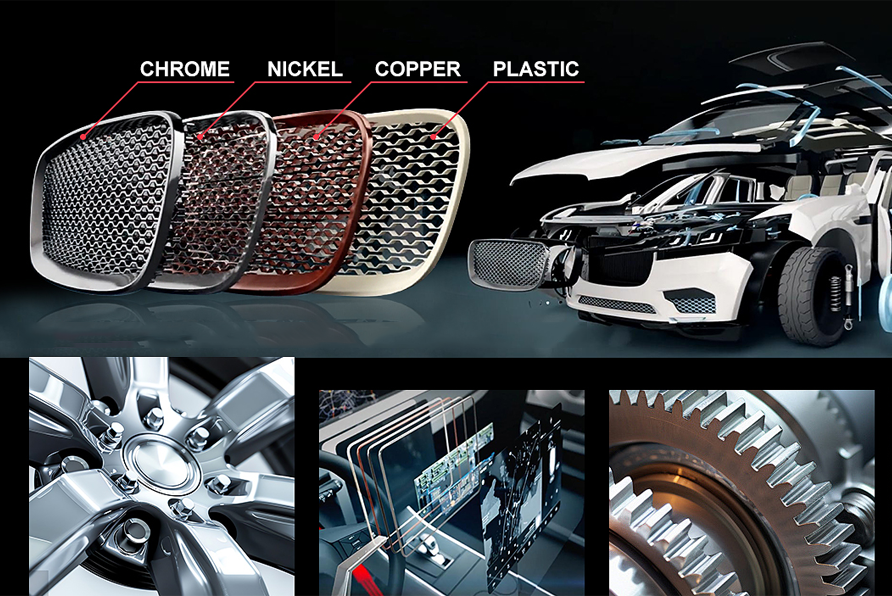
Recommended products for Electroplating Surface Treatment
Cooling Type for Electroplating
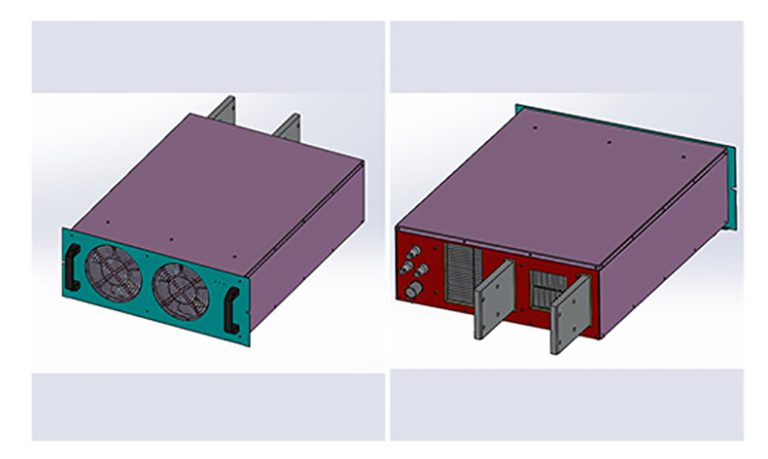
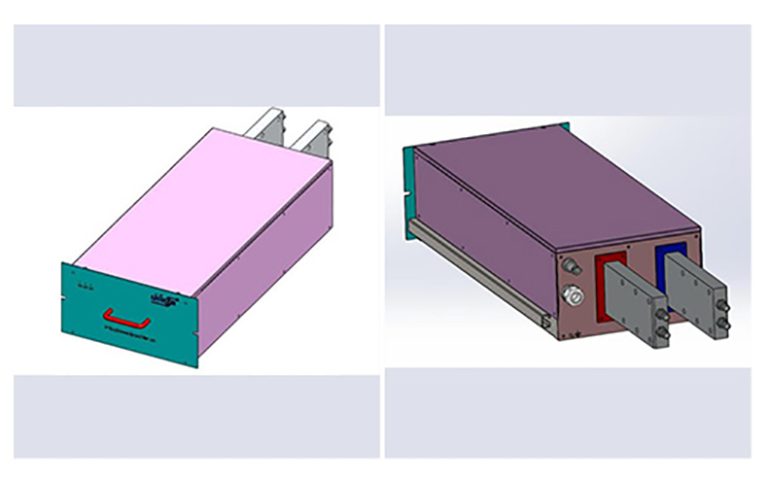
Recent Application Cases
Stay updated with the latest cases and projects.
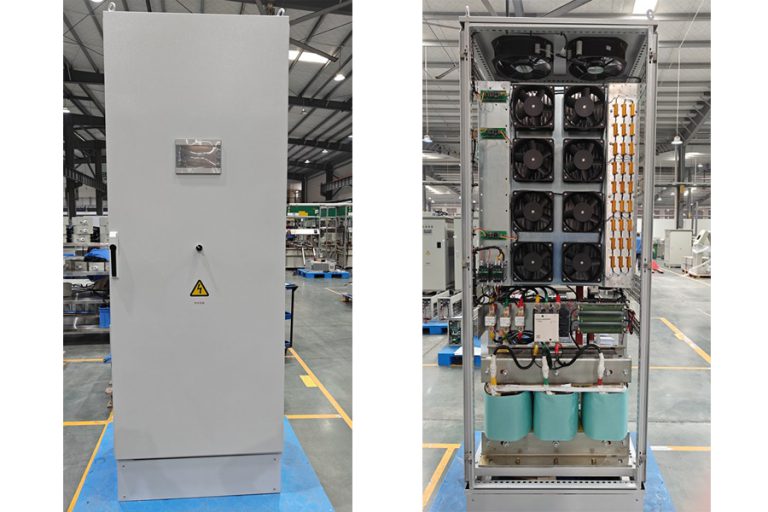
Advanced Plasma Coating Rectifier Solutions in China
200V 500A Plasma Plating Rectifier Chopper technology rectifier for plasma coating, IGBT chopper output current…
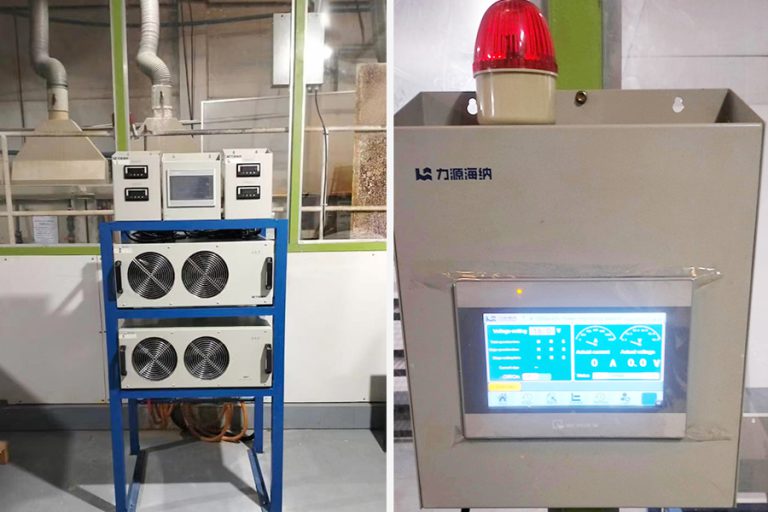
Metal Plating Project in Thailand
A metal metal plating project in thailand successfully addressed technical challenges in chromium plating…
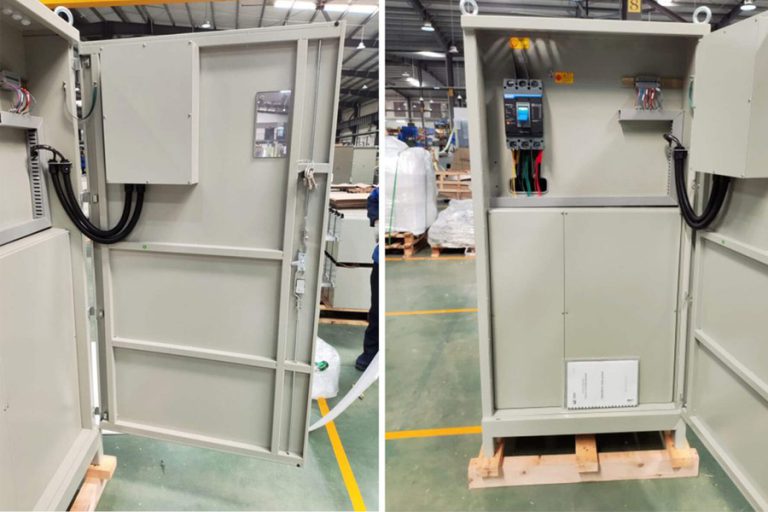
Electrophoretic Coating in Iran
Electrophoretic Coating in Iran Project:KGFB-320A/400V Rectifier (Output Voltage: 0~400VDC, Output Current: 0~320A) for Industrial…
Hot Products
-
Factory Price 2000A 15V Nickel Plating Rectifier
-
Factory Price 1200A 15V Rectifier for Zinc Plating
-
Z360A 8V F1080A 24V PCB & Metal Finishing Pulse Plating Rectifier
-
120A ±50V Pulse Plating Rectifier
-
500A ±20V Hard Chrome Plating Rectifier
-
Factory Price 7200A 50V Plating Power Rectifier for Sale
-
200A 350V Electroplating Power Supply for Surface Plating Rectifiers
-
Factory Price 1500A 12V Zinc Plating Rectifier for Sale
Welcome to visit
Welcome to contact us for further discuss if you are interested in any of our products. » Get Product Catalog