Product Knowledge Base
An electroplating rectifier serves as a critical power conversion system within metal surface treatment processes. By transforming alternating current into precisely controlled direct current, this equipment enables essential industrial applications including chromium deposition, nickel coating, and copper plating. Unlike standard power supplies, these specialized rectifiers deliver tailored electrical parameters to meet the exacting demands of electrochemical deposition processes.
Key operational advantages distinguish modern electroplating rectifiers in industrial settings. Their advanced conversion architecture ensures rapid AC-to-DC transformation while maintaining exceptional output stability – a crucial factor for achieving uniform plating thickness and material adhesion. Energy efficiency stands out as a hallmark feature, with contemporary models demonstrating up to 95% conversion efficiency through innovative switching technologies and intelligent power management systems.
Operators benefit from sophisticated regulation capabilities that surpass basic voltage/current adjustments. Digital control interfaces allow micron-level precision in parameter settings, with real-time feedback systems automatically compensating for process variables. This dynamic adjustability proves particularly valuable when handling complex workpieces or transitioning between different plating bath chemistries.
Durability constitutes another critical design focus. Industrial-grade components rated for continuous operation ensure reliable performance in challenging workshop environments. Corrosion-resistant enclosures with IP54-rated protection safeguard internal circuitry from plating solution vapors and particulate contamination. Advanced thermal management systems combine passive cooling with variable-speed fans to maintain optimal operating temperatures.
Safety integration reaches new levels in current-generation models. Comprehensive protection mechanisms extend beyond basic overload safeguards to include phase failure detection, electrolyte leakage monitoring, and automatic short-circuit interruption. These features work in tandem with ground fault protection systems to create multiple layers of operational security.
Maintenance requirements have been significantly reduced through modular component design. Hot-swappable power modules and tool-free access panels facilitate rapid servicing, while self-diagnostic systems provide clear fault code indications. This service-oriented design philosophy minimizes equipment downtime and simplifies technician training requirements.
The evolution of electroplating rectifier technology continues to address emerging industrial needs. Recent advancements incorporate regenerative power systems that recover energy during process interruptions, along with IoT-enabled models providing remote monitoring and predictive maintenance capabilities. These innovations position electroplating rectifiers as smart manufacturing components within Industry 4.0 production ecosystems.
Electroplating rectifiers are vital for metal deposition processes by delivering regulated DC power from standard AC sources. Their core role involves transforming alternating current into precisely controlled direct current essential for consistent ion transfer during plating.
Core Operations:
These systems perform two fundamental tasks. First, they alter the electrical current’s directionality using semiconductor components. While standard wall outlets provide bidirectional AC flow, plating demands unidirectional electron movement for proper metal ion deposition. Second, they enable fine-tuning of electrical parameters through advanced regulation circuits. Operators can adjust output characteristics to achieve specific coating properties and deposition rates.
Working Methodology:
The conversion process begins with directional control elements like diodes or thyristors. These components act as electrical gatekeepers, permitting current flow in only one direction. When AC input passes through these semiconductor devices, the output becomes pulsating DC. Subsequent filtering stages using capacitors and inductors smooth these pulses into stable, low-ripple current.
Modern units incorporate multiple control layers. Microprocessor-based systems continuously monitor and adjust outputs, compensating for line fluctuations and load variations. Safety mechanisms protect both equipment and workpieces through current-limiting circuits and fault detection systems. Advanced models may include waveform shaping capabilities for specialized applications.
Critical performance aspects include conversion efficiency (typically 85-95% for quality units), output stability (±1% voltage regulation), and thermal management. Proper heat dissipation through air or liquid cooling maintains component reliability during extended operation. Interface designs vary from analog dial controls to digital touchscreens with recipe storage and process logging.
By maintaining strict electrical parameters and stable output characteristics, these power conversion systems enable reproducible metal deposition with controlled thickness and microstructure. Their operation directly impacts plating quality factors including adhesion strength, surface smoothness, and corrosion resistance in finished products.
A hard chrome plating rectifier functions as an essential power conversion system for surface treatment applications. This equipment comprises two primary components: a rectification unit and filtering components, working in tandem to transform alternating current into regulated direct current.
The rectification unit performs the fundamental AC-to-DC conversion through a bridge circuit configuration. Four diodes arranged in a bridge pattern alternate conduction paths during each AC cycle’s positive and negative phases. This configuration ensures unidirectional current flow by redirecting both halves of the AC waveform into consistent polarity output.
Filtering components maintain current stability following rectification. Capacitive elements smooth the pulsating DC output by absorbing peak voltages and releasing stored energy during low-voltage intervals. This action effectively reduces residual ripple voltage, critical for maintaining consistent plating quality in hard chromium deposition processes.
System operation follows sequential energy conversion stages: incoming AC power undergoes full-wave rectification through the diode bridge, followed by capacitive filtration to stabilize DC characteristics. The resulting steady direct current meets the precise electrical requirements for depositing uniform chromium layers on substrate materials.
High Efficiency
IGBT has low conduction loss and switching loss, which can achieve efficient energy conversion and is suitable for high-precision and high reliability requirements such as electrolytic copper. Under low voltage and low current conditions, the efficiency is higher than that of thyristors.
High Precision
Through PWM control, the output voltage and current can be precisely adjusted to meet the strict requirements of the electrolysis process. Quickly respond to load changes and reduce voltage fluctuations.
Modular Design
IGBT power supply adopts modular design, which is easy to maintain and expand. Modular design improves the reliability and flexibility of the system, reducing maintenance costs.
Recent Application Cases
Stay updated with the latest cases and projects.
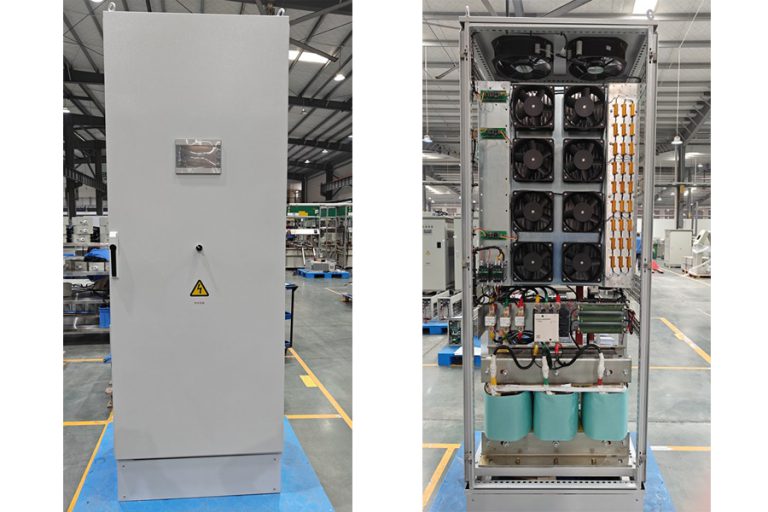
Advanced Plasma Coating Rectifier Solutions in China
200V 500A Plasma Plating Rectifier Chopper technology rectifier for plasma coating, IGBT chopper output current…
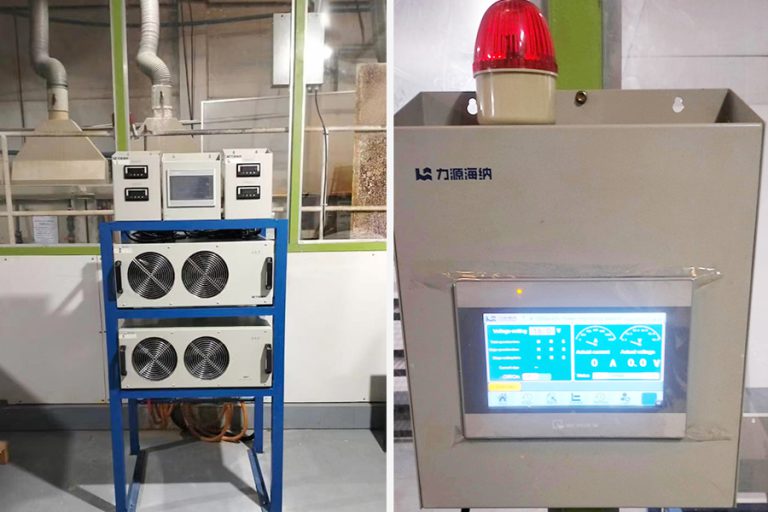
Metal Plating Project in Thailand
A metal metal plating project in thailand successfully addressed technical challenges in chromium plating…
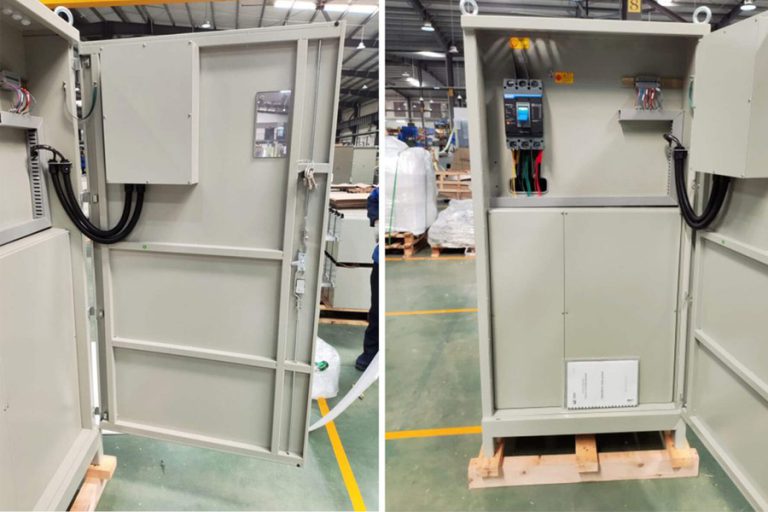
Electrophoretic Coating in Iran
Electrophoretic Coating in Iran Project:KGFB-320A/400V Rectifier (Output Voltage: 0~400VDC, Output Current: 0~320A) for Industrial…
Business inquiries
Are you interested in one of our products? Please use our inquiry form or leave a message, and we’ll respond within 24 hours.